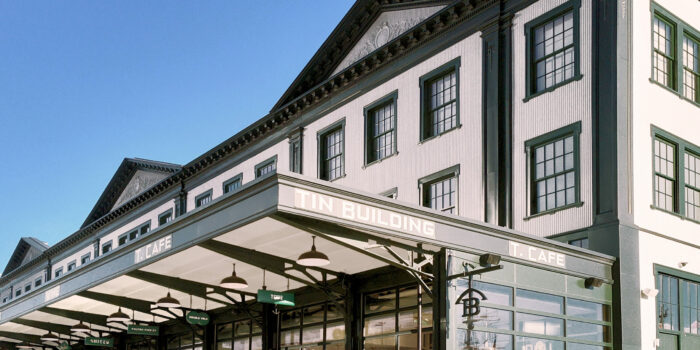
Start the Presses: Roll Forming vs. Press Braking
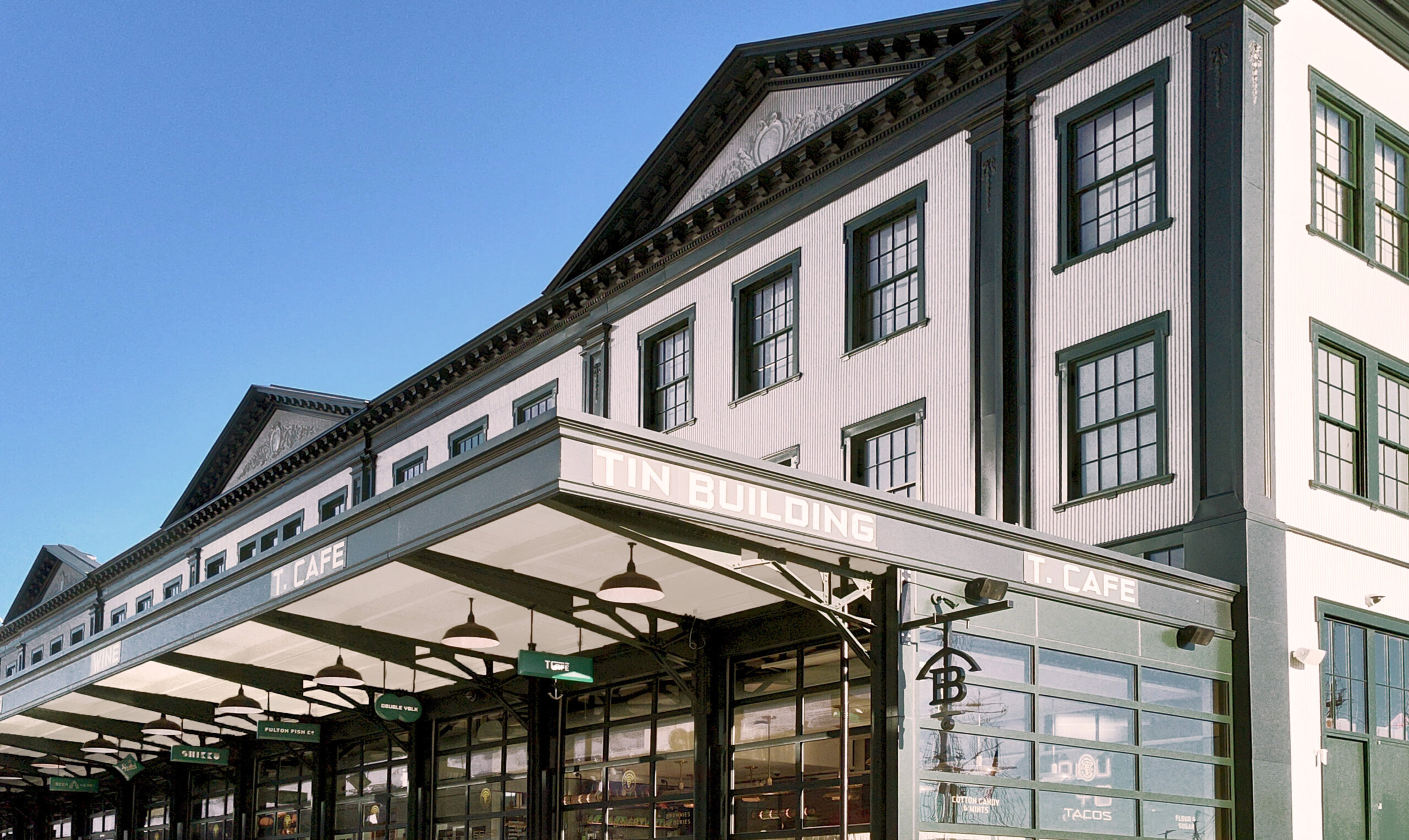
Identifying the Benefit of Press Braking
Metal is a critical part of bringing architectural creations to life. From structural components to reinforcements, roofing, windows, and more, metals are widely used in the building and construction sector.
When it comes to fabrication techniques, there are two popular methods that stand out: press braking and roll forming. Each approach has characteristics that make them suitable for particular applications that will cater to specific needs. However, when custom profiles are desired, there is one tried and true method that enables specifiers to achieve exactly what they need.
For these types of custom jobs, the solution for achieving bespoke metal products is press braking.
Roll Forming Basics, and Limitations
Roll forming is a metal fabrication technique that involves feeding a coil of material through a series of offset discs to shape it into a specific profile. Consider the corrugation of a piece of cardboard but on a much larger scale and with heavier duty materials. Nonetheless, the concept is the same, and the end result might look something like this. This method is useful for large scale production runs of ready-made, off-the-shelf products.
While roll forming offers efficiency in mass production, it is limited by material thickness as well as the variety of profiles it can achieve. In addition, the process lends itself to pre-finished, thin gauge metals, which limits the finish types that can be applied. Since roll forming is a continuous coil process, the entire roll must be finished before it comes off the coil and into the roll forming machinery.
Finally, roll formed products and profiles provide less customizability and will end up being less rigid because of material thickness maximums.
As a practical matter, roll forming is limited to specific profiles and finishes, restricting the range of design possibilities, potentially stymieing the design visions of architects or building owners.
Press Brake Versatility
Press braking offers architects and owners much more versatility when it comes to fabricating metal profiles. The process can still be used to achieve standard looks. However, it comes in handy when a designer draws up a profile that is not already in a roll forming fabricator’s catalog. In this scenario, choosing a fabricator with press braking capabilities helps achieve unique angles, sizes, and dimensions because each bend is completed one by one.
Aluminum used in press braking tends to deliver a higher quality end product because it can process thicker materials. Therefore, once installed on a building, the chance for waving, bending, or oil canning is significantly diminished. The final product is much sturdier, offering greater durability over the lifespan of a structure.
Case in Point – Tin Building
The revitalization of the historic Tin Building in Manhattan was a high-profile job that required the use of custom metal panels for the building’s exterior. The development – aimed at offering some of the most iconic, modern dining experiences in New York City –needed a built-to-last facade.
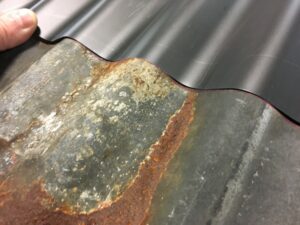
The project team selected aluminum panels that SAF fabricated using the press braking technique to get the specific shape the project team desired. In total, the building uses 17,000 square feet of cornice materials; 2,500 square feet of pilasters; 10,000 square feet of window and door frames; and 30,000 square feet of aluminum wall panels. The project also featured an additional 10,000 square feet of other mill finish items. All metal materials on the project needed particular bends and shapes. As a result, all were formed using the press brake.
Shaping Possibilities
The choice between press braking and roll forming is ultimately dependent on project needs, budget, and the desired finish. However, construction industry pros searching for high-quality aluminum products made to intricate, custom profiles should explore the possibilities of press braking.
The ability to shape metal profiles into classic or modern shapes makes press braking a valuable production process for architects, designers, and owners. In addition, this method’s capacity to work with thicker gauges of aluminum and ability to accommodate pre-finished or post-finished metal further solidifies its position as a preferred metal fabrication process for those seeking to take building design to new heights.
Using press braking, the expert craftsmen at SAF’s production facilities across the country are creating bespoke metal profiles for a range of commercial construction needs.