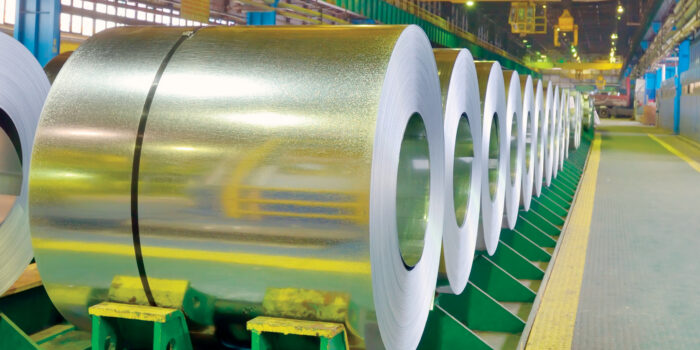
Coil vs. Batch Anodizing
Your Guide to Anodizing: The Superior Metal Finishing Process
Anodizing is a one-of-a-kind metal finishing process that delivers longevity, durability, and aesthetic appeal to aluminum products. There are two primary methods—batch anodizing and coil anodizing—and they cater to distinct needs within the construction space. Each possesses unique advantages, and there are important considerations depending on a customer’s desired final product and the application at hand.
Batch Anodizing: Artistry Meets Precision
Batch anodizing involves immersing individual parts, such as sheets, extrusions, and fabricated components, into a series of anodizing tanks. Aluminum parts are clamped onto racks and then submerged into sulfuric acid tanks, where an electrical current is applied to form a durable, porous anodic oxide surface on the metal. These tanks, which include etching and anodizing baths, play a crucial role in building up a resilient and uniform coating. Unlike paints or powder coatings, anodizing interacts and alters the chemistry of aluminum to provide one of the most durable finishes for architectural products. However, from a labor perspective, racking and unracking individual parts adds to the amount of manual labor required to complete the process.
With high-mix, low-volume batch anodizing, experienced operators are essential, making the process much more of an art form compared to coil anodizing. Batch operators must meticulously monitor variables to achieve specific colors and coating thicknesses. Automated batch lines are also available, but these are best suited for a low-mix, high-volume product line and require a significant capital investment. Most job shops use the more labor-intensive method, where the end product can be subject to color variations due to the manual nature of the process. In some cases, this variation is a desired outcome for architectural applications where slight tonal differences are preferred as an artistic choice.
Coil Anodizing: Consistency in Continuity
Conversely, coil anodizing is a continuous process where an aluminum coil is pulled through a series of rollers and a number of anodizing tanks. Compared to batch, this method offers greater consistency in finish due to the continuous nature of the operation. Large-scale aluminum coils unravel into the baths, become anodized, and are finally rolled back into a coil on the other side of the tanks. Each portion of the material spends the exact same amount of time in the anodizing bath.
This process is less labor-intensive and provides a reliable and uniform coating. Coil anodizing is best suited for thinner materials that can be rolled tightly into a coil. Anodizing thicker aluminum coil poses risks of finish fracturing during the recoiling process post-anodizing.
Rigid materials with bends, welds, or three-dimensional shapes cannot be coil anodized. For that, batch anodizing is the right method.
Coil anodizing is particularly suited for high-volume production because once it is set up, the rest of the process is automated. Compared to batch anodizing, coil is quicker, more efficient, and requires less labor.
Time, Tanks, and Thicknesses
For anodizing, SAF uses 5005 alloy, which is a specific anodizing-quality coil purchased from mills and ideal for architectural applications. Customers can also send SAF other non-anodizing-quality alloys that only need oxidation protection or an anodized finish for caulk adhesion. In this scenario, aesthetics are not a concern since the material will not be used for public-facing architectural use, so using anodizing-quality 5005 alloy is less important.
The time requirements for anodizing largely depend on the desired coating thickness. Batch anodizing allows for precise control over thickness, with a general guideline of 20 minutes yielding approximately 0.3 mils, 30 minutes for 0.4 mils, and 50 minutes for 0.7 mils. 0.7 mils is the minimum requirement for Architectural Class I anodic coatings.
How fast a coil line moves will vary based on the thickness of the aluminum and the desired thickness of the anodized finish. Thicker materials must be programmed by the operator to move more slowly through the tank in order to build up the proper protective coating.
To ensure quality, SAF uses a HunterLabs colorimeter to assess the three-dimensional quality of color for both coil and batch anodized aluminum. When customers require a specific color other than what industry tolerances allow, colorimeter records can be used to confirm it meets the specified tolerance.
The Final Word
Batch anodizing offers a level of artful precision, allowing operators to fine-tune colors and coating thicknesses. It is ideal for fabricated parts that cannot be anodized using the coil method. However, keep in mind that batch is prone to color variation, is more labor intensive, and is costlier because of setup requirements, manpower for racking, and ongoing supervision. Regardless, it is the preferred method for thicker materials or anything with welds, bends, or corners.
With its continuous operation, coil anodizing provides a more consistent finish and is less labor-intensive, tending to be more cost-effective. It is suitable for thinner materials and has limitations when trying to achieve a thicker anodized coating.
Understanding the strengths and limitations of each process empowers fabricators, architects, and other construction stakeholders to make informed purchasing decisions for anodized aluminum that will meet the functional and aesthetic requirements of their specific applications.
Questions about anodizing for your next project? Reach out today and let the anodizing experts at SAF help you get started.